The Fabrication Workshop is a dedicated space for PCB boards manufacturing, soldering and minor hardware setups dedicated to circuits arrangements.
The manufacturing capabilities includes the production of single or double-sided printed circuit boards (PCB) for rapid prototyping. The boards are typically produced on standard FR4 1.6 mm glass fiber epoxy laminate material.
The following equipment is employed for the PCB manufacturing:
LPKF ProtoMat C100 HF plotter is especially designed for RF and microwave PCBs. A motor speed of 100,000 rpm allows the widest range of tools, including 0.15 mm (6 mil) endmills for high-performance designs. A contact-less air bearing depth limiter is ideal for use on flexible or gold – plated circuits. Micrometer depth adjustment can be used to mill precise pockets into brass or aluminum-backed circuits, or to route beryllium copper sheets. The ProtoMat C100/HF is fully compatible with multilayer applications and all common materials.
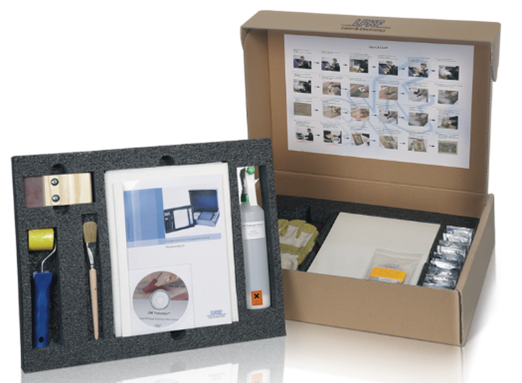
LPKF ProConduct is a chemical-free through-hole plating process for double-sided printed circuit boards. All vias are coated with a specially developed paste by using a squeegee and a vacuum table. The conductive paste allows the metallization of through-holes with a diameter of up to 0.4 mm and an aspect ratio of 1:4.
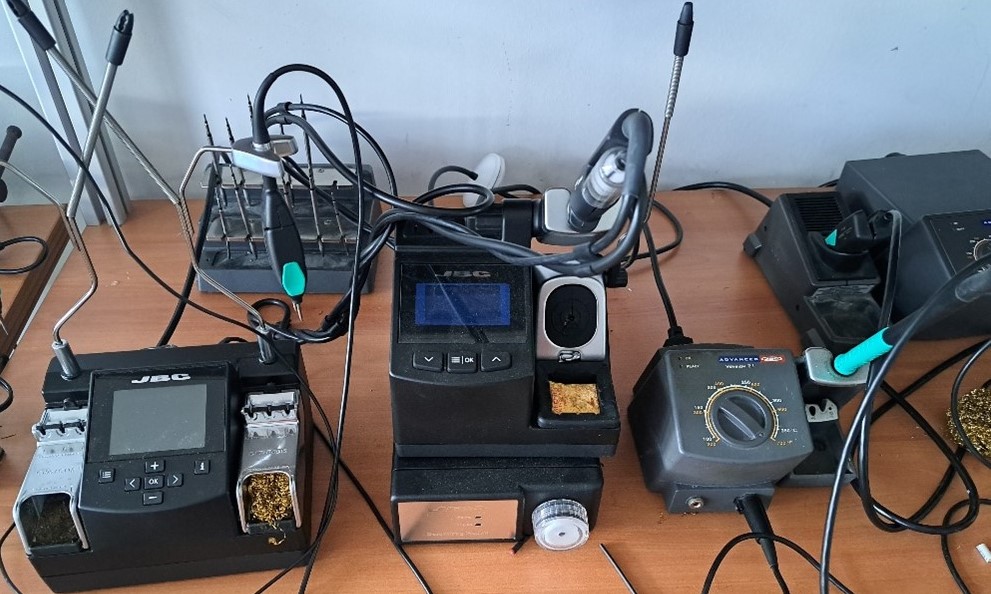
The soldering JBC stations include soldering tools of different sizes, with nano tools and microscope for high precision tasks. Rework stations include special tweezers and desoldering irons for removing tin and components. In addition, there is a hot air station for soldering and resoldering circuits where the iron tools are not a good choice. The working table includes additional tools, such a light with magnifying lens, basic screwdrivers, wire cutters, tin rolls and chemicals used in soldering procedures.